General – Hydrogen Gas Storgae
HYBRIT’s pilot project for hydrogen gas storage has now been completed and reported to the Swedish Energy Agency.
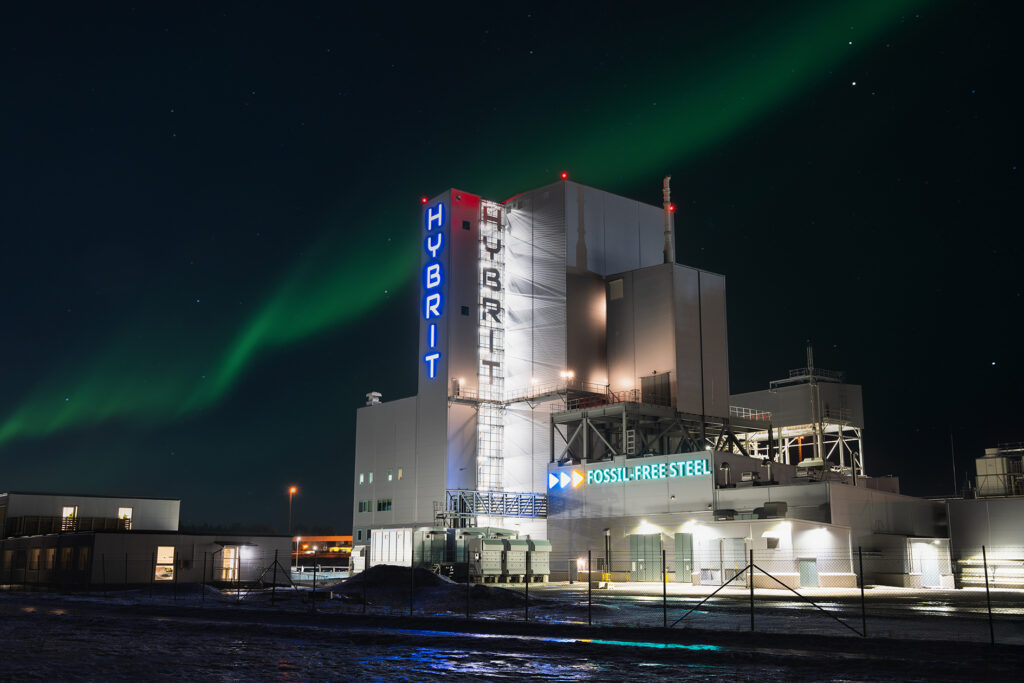
The results show that it is technically possible to store fossil-free hydrogen gas for producing fossil-free iron and steel on an industrial scale. This can also reduce the variable operating costs of hydrogen production by up to 40 per cent.
The HYBRIT initiative was launched in 2016 by owners SSAB, LKAB and Vattenfall to develop the world’s first fossil-free, ore-based iron- and steelmaking using fossil-free electricity and hydrogen gas. The project for the production of fossil-free sponge iron for steel production (DR pilot) is now being followed up with the results of the pilot for fossil-free hydrogen gas production and storage.
The project has successfully designed and constructed a 100 m3 hydrogen storage facility based on steel-lined rock cavern technology in Svartöberget adjacent to the DR pilot for sponge iron production in Luleå, Sweden.
The tests now completed show that the technology works to support a large-scale hydrogen user, and that savings of about 25-40 per cent of the variable operating costs of hydrogen gas production could be reached. The pilot storage facility has undergone accelerated mechanical testing equivalent to approximately 50 years of operation, and the safety, functionality and performance of the facility have been successfully demonstrated.
“The pilot project has been highly successful and has given us the results we hoped for. We have shown that it is possible to use this technology to increase the flexibility of the electricity system and that it is a safe design that lasts over time. Hydrogen gas storage is an important piece of the puzzle to electrify industrial processes while increasing the amount of weather-dependent power. With the results and experiences gained from the pilot project, the technology is now ready to be scaled up,” says Mikael Nordlander, Director, Industry Decarbonisation at Vattenfall’s Industrial Partnerships.
Future fossil-free industrial processes using hydrogen gas from fossil-free electricity instead of fossil fuels will mean that industry will be more dependent on the electricity system. In this case, it is crucial to secure the supply of hydrogen. The purpose of a hydrogen storage facility is primarily to be able to adjust hydrogen production to electricity market fluctuations. Hydrogen gas production costs are optimised by producing and storing surplus hydrogen gas when electricity prices are low and reducing production and using the stored hydrogen gas when prices are high.
“Hydrogen is an important part of LKAB’s future strategy and journey towards carbon dioxide-free products and processes. We have yet to make any decisions on hydrogen gas storage, but the successful results from the pilot give us good conditions when we review the needs and opportunities for storage in conjunction with our planned sponge iron production facilities,” says Jenny Greberg, Vice President of Technology at LKAB.
“The results from the HYBRIT pilot project show that large-scale storage of fossil-free hydrogen is technically possible and economically beneficial. With these innovative technologies, we can build strong fossil-free value chains with the potential of drastically reducing the climate footprint of the iron and steel industry,” says Martin Pei, CTO at SSAB.
The steel industry currently accounts for around 7 per cent of global carbon dioxide emissions. The HYBRIT technology will enable SSAB to reduce Sweden’s and Finland’s carbon dioxide emissions by 10 per cent and 7 per cent respectively.